Solution for series production / threath
High performance tapping attachments with integrated reversing gear
Application
Application: tapping, roll forming
Machine type: machining centres and special purpose machines
Features
- self reversing gear
- direct collet location
- damping elements between drive key in the spindle and the coupling sleeve
- balls used in the couplings elements
- hydrostatic pressure compensation for IC version
- constant tapping speed (through built- in reversing gear)
- exchangeable drivers BN17…
- built-in length adjustment screw
- sealed, stable version of the stop arm
Advantages
- reversing of machine spindle not required - shortest processing time possible, minimum time saving 200 – 400 ms per thread, substantially less electrical power consumption
- high concentricity - better life time of the tool, reduced wear, less unbalanced mass
- avoiding premature wear - less maintenance intensive
- exact disengaging point - exact thread depth, high repeat accuracy
- no axial movement of the spindle into tension, even when the coolant flow is blocked - no risk of collision through extended tool
- ideal cutting conditions - longer tool life time
- positive torque transmission of the tap and of the driver in the spindle - no twisting or slipping of the tap in the collet
- taps can be set to the required length - no input data error of tool length in machine offset (no risk of collision)
- no malfunction due to contamination or through too much gap in the stop arm - reduced down time of the machine, prevention of collision / no damage from displaced stop arm
Success Story GNCK
Reduction of machining time: Cut down to half
Mission
- Workplece: M8 DIMagnesium eletric housing
- Machine: FEELER QM-40SA
- Batch size: 528 parts / day
Cutting data:
- n=3000 rpm programmed
- n=2000 rpm (max. reached)
- f= 1500mm/min
- 19 threads per part, M3x0,5,
- 10mm deep
Machining time:
- Snchronized
- 3min 20sec.
Downloads
Solution
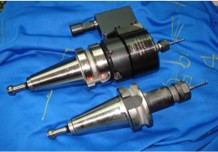
Cutting data:
- n=3000 rpm
- f= 1425mm/min
- 19 threads per part
- M3x0,5 10mm deep
Machining time:
- No change of spindle direction
- 1min 40sec.
Customer benefit
Reduction of machining time: Cut down to half!
Costcalculation:
Reduction of machining time
About 0,833 min./ part
Batch size: 528 parts / day
Machine hour rate: 50 € / hour
Costreduction:
366,50 € / day; 91625€ / year (250 workingdays / per year)
