APPLICATION
Application: Automotive, general Mechanical Engineering, Renewable
Machine type: machining centres, CNC-turning and special purpose machines with synchronized feed
for the tapping operation
Features
- Minimum length compensation in compression and tension direction
- Ball bearing mounted (i.e. torque independent) suspension
- Suitable for internal coolant supply up to 80 bar
- Suitable for taps and thread formers
- Suitable for right-hand and left-hand threads
- Optimized spring-damper technology (± 0.5mm)
- 3D Synchro completely encapsulated function chamber (washable up to 80°C)
- Optimized seal (comparable to IP68)
- 100% SCK-kompatibel
Advantage
- Reduction of the pressure on the thread fl anks Compensation of synchronization errors
- Compensation of synchronization errors
- Higher process stability
- Longer tap life
- Better thread quality
Tool presetting via axial adjustment screw possible from both sides
(screw is not included in the scope of delivery)
Best application
You can use our 3D-Synchro chuck as a collet chuck
for driven tool holders as well as for direct clamping
in machine spindles.
- 220%*1 higher stand Quantitiy of the Tap
- 200%*2 higher out speed
- 80 BAR coolant pressure (instead of 50 BAR)
*1 220% tool life of M8 tap in endurance test at n= 560 min-1 in X37CrMoV5-1 (Rm= 770 N/mm2) with the S3D Synchro chuck compared to 100% tool life with a standard collet holder.
*2 200% cutting speed = 25 m/min with M10 tap in grey cast iron GG20 (Rm > 200 N/mm2) with the S3D Synchro chuck compared to 100% = 12.5 25 m/min with a standard collet holder while
maintaining thread quality and tolerance. With the standard collet chuck, the cutting speed could not be increased, otherwise the threads would no longer be within tolerance.
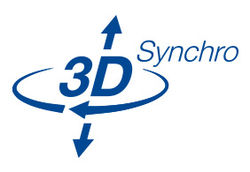
The elastomers used are dimensionally stable and resistant to all
coolants/lubricants. Due to the defi ned length compensation,
plastic deformation of the damping elements is excluded.
This results in consistent cutting behavior over the entire life of the tool.
Higher process stability - better thread quality - longer service life
The latest generation S3D- Synchro chuck has been adapted to the current market requirements.
Tool presetting is possible from the machine side and the tool side, the lubricant feed-through
has been optimized, thus ensuring a leakage-free transfer to the tap.
The length compensation on compression and tension (e.g. +/- 0.5 mm), as well as the damping
in the direction of rotation compensate for the smallest synchronization errors and position deviations.
This reduces the pressure on the on the thread fl anks of the tool is reduced and the required cutting torque is minimized.