MQL clamping tools
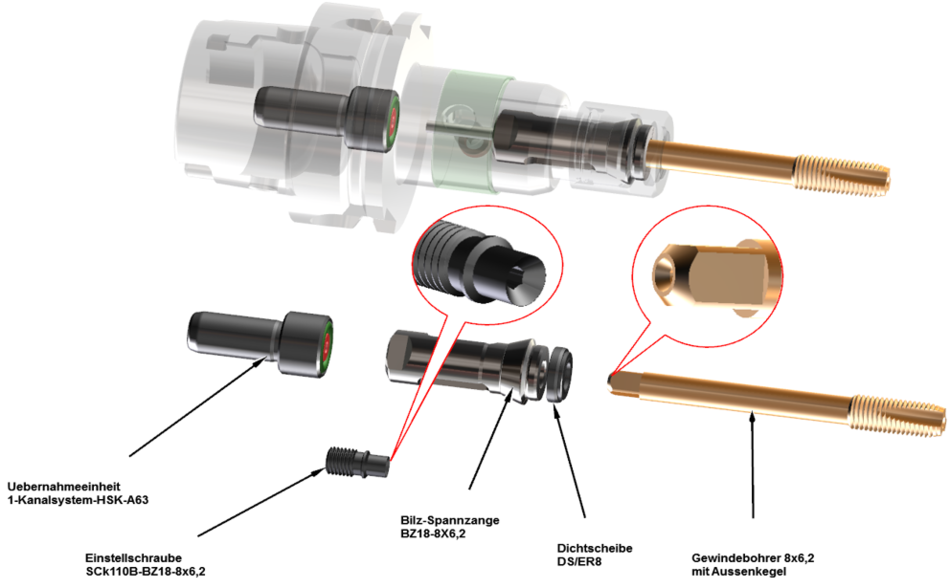
![[Translate to USA:] [Translate to Englisch:] Bilz ThermoGrip MMS Schrumpffutter](/fileadmin/_processed_/0/e/csm_t1600_MMS_hsk63_Schrumpffutter_01_b9f35797c5.png)
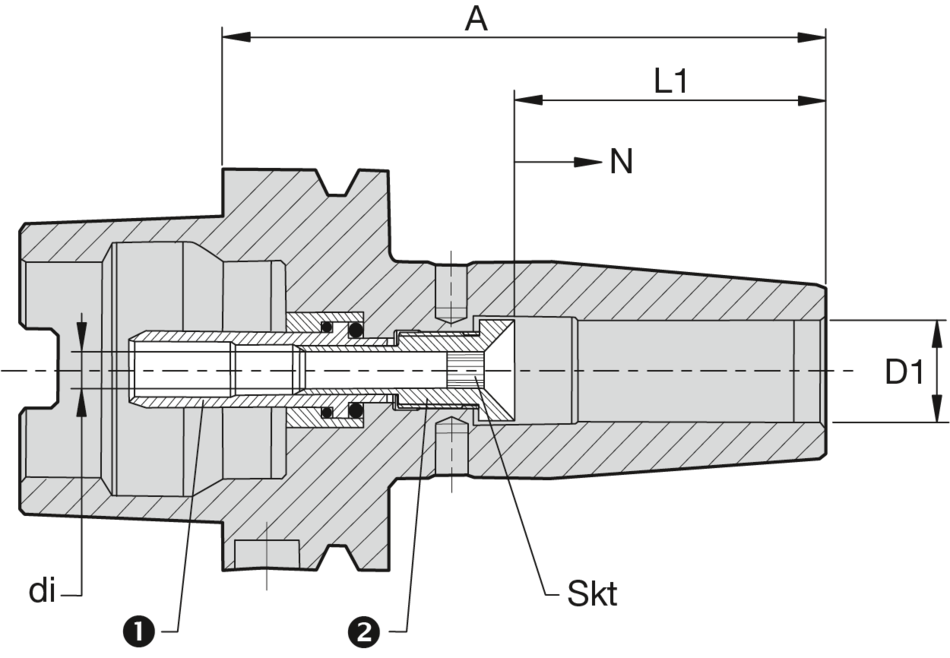
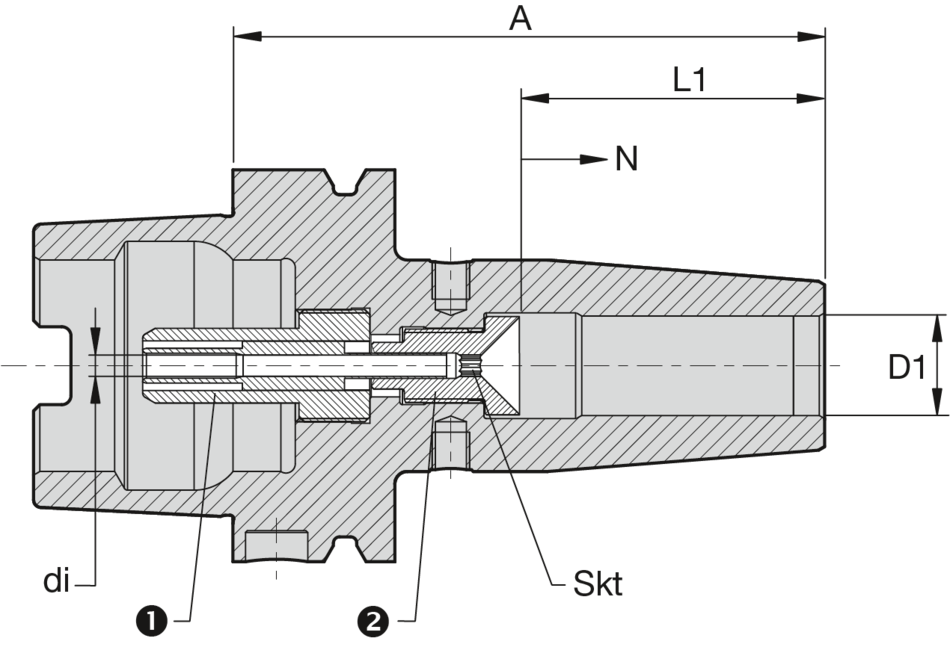
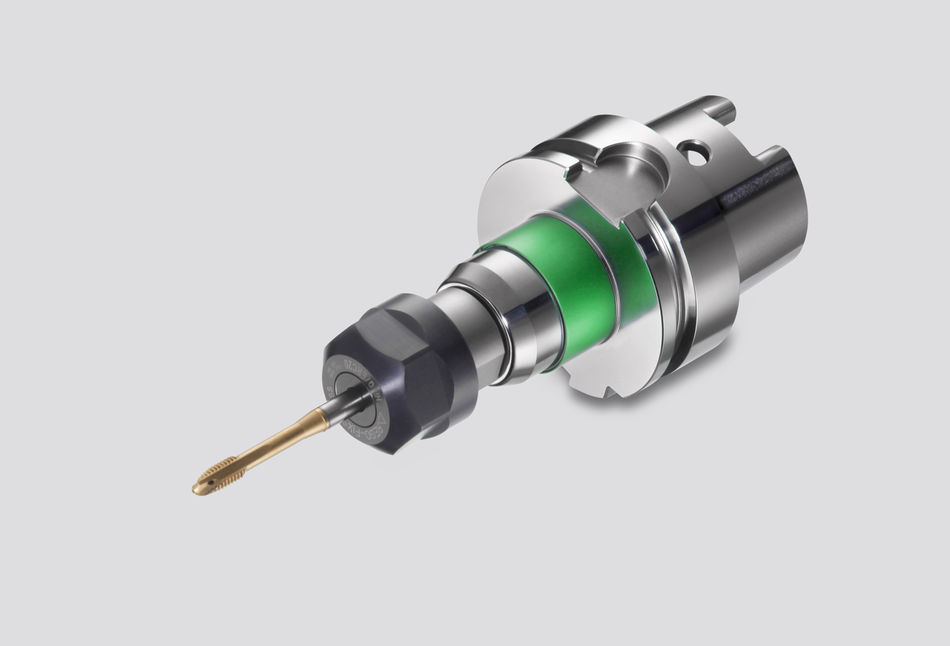
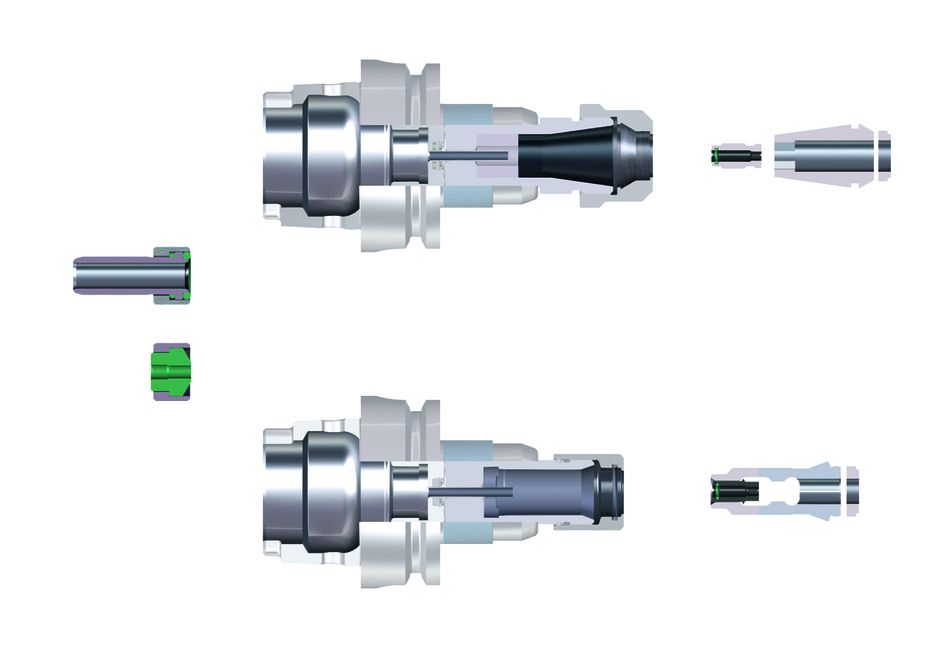
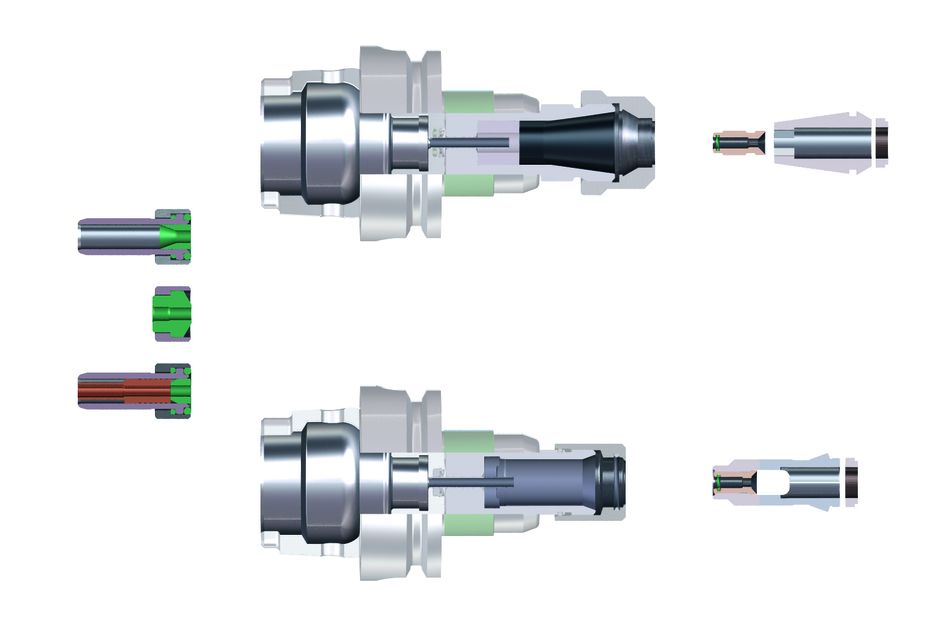
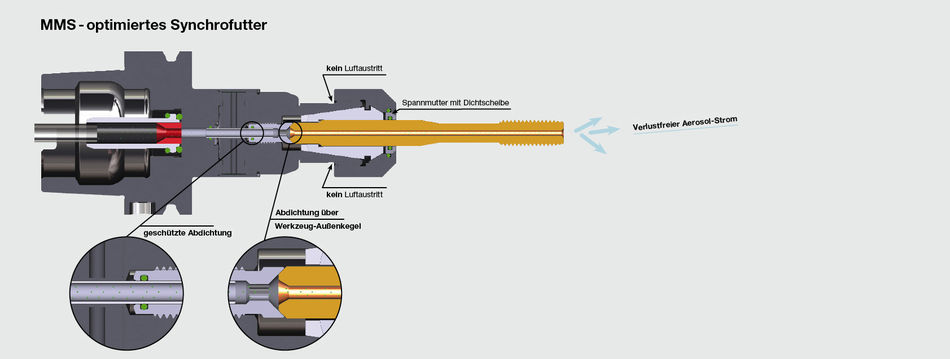
MQL - the new performance class of MQL compliant clamping systems
Lubricant from the very first moment – loss-free!
MQL and Clamping Tools
Only the smallest amounts of lubrication are used in connection with MQL clamping tools - the application revolves around correct delivery of coolant to the cutting edge without any drop in pressure. The MQL compliant clamping tool plays a decisive role as part of the MQL delivery system.
Future-proof technology by acquiring the HORKOS license
MQL stands out due to an enormously reduced consumption of lubricants in use compared to conventional wet machining.
There are two basic challenges for the clamping tool:
a) Optimised leak-proofing for a leak-free aerosol stream with no fine mist of aerosol droplets, no build up of moisture in the clamping chuck
b) Lubrication delivery from the very first moment for a flawless aerosol flow without any drop in pressure to the cutting edge
The new MQL generation from Bilz fully meets these requirements.
Optimised leak-proofing of our synchro chucks is unique on the market so far and a patent was applied for in January 2010.
Synchro chucks SCK - the next generation
Process optimization by innovation
The minimum length compensation on pressure and retraction (+/-0,15 mm) as well as the radial damping compensate minimum deviations in position and discrepancies between the actual feed and the pitch of the tap. The flank pressure and therefore also the abrasion at the thread flanks is reduced considerably.
Combined solution MQL, IC + without coolant - one chuck is sufficient
Combined solution MQL, IC + without coolant - one chuck is sufficient Independent of cooling and lubricant type, the newSCK is suitable for:
• MQL 1-channel/ - 2-channel (optionally)
• IC up to 50 bar coolant pressure
• dry processing
• machines with manual and automatic tool changing
Combined solution two-way length compensation - literally one move
Independently of the collet, the length compensation can now be effected either from the collet side or from the holder side – one move instead of time consuming readjustment
Compact deisgn - even more security
Tool life increases up to 100% because of constantly high quality cutting performance, process security and an easy handling:
• high idle running speed up to 15.000 min-1
• compact construction
• dimensionally stable and very resistant elastomere
• minimal length compensation (pressure/retraction +/- 0,15 mm)
Think ahead! Future-proof minimum quantity lubrication with BILZ
The minimum quantity lubrication (MQL) process is becoming increasingly important. As a reliable partner to its customers, BILZ is already securing access today to the technologies of tomorrow and has acquired the licence for the connection in the chuck from HORKUS in Japan. In the following article, we explain why this machine/tool interface is of central importance. ....More/Further
Think ahead! Future-proof minimum quantity lubrication with BILZ
The process of minimum quantity lubrication (MQL) has become increasingly important in machining in recent years. MQL basically refers to the lubrication of machining processes with small quantities of lubricant. The advantages in machining are obvious:
-Loss-free aerosol flow right up to the tip of the tool
-Delay-free flow of the aerosol without pressure drop
-Flexible systems for thread cutting systems and shrink-fit holders
-Future-proof technology through acquisition of the HORKUS licence
The MQL uses an air/oil mixture that prevents the generation of frictional heat by optimising lubrication. The remaining heat is dissipated via the tool and the chip. Historically, the supply of coolant from the outside via the machine through the chuck replaced the supply of coolant from the outside when cooling the machining area. The internal coolant supply (IC) was born and essentially consisted of water with a small amount of lubricant, channelled through at a pressure of 50 to 80 bar. However, the experience of large-scale manufacturers showed that the IC accounted for up to 15 per cent of the production costs. This gave rise to the idea of MQL, as the "normal" consumption of several hundred litres of water per hour was not ecologically and economically sustainable. The lubricant was now only added in small quantities and the water was simply omitted. Instead of the cooling lubricant, for example, only the lubricant oil is used, which is supplied as a finely atomised mist (aerosol) at a pressure of 6 to 10 bar. Today's MQL systems have a consumption of less than 100 millilitres per hour, some even less than 10 ml.
BILZ offers 1- and 2-channel systems
MQL technology is divided into two systems; BILZ offers both systems for synchronised and shrink-fit applications: There is the external MQL feed, in which the minimum quantity is fed to the mould or the effective point through a nozzle installed in the machining area of the machine. And the inner MQL feed, where this is fed through the work spindle, the tool holder and the tool directly into the cutting edge. This enables optimum wetting at the point of contact. MQL systems are divided into 1-channel (premixing of the aerosol outside the spindle) and 2-channel (premixing directly in the spindle) processes. Nowadays, the 1-channel technology is clearly in the lead. The aerosol is atomised so finely that it practically does not separate. This means that even longer supply lines and "corners" are no longer a problem, not to mention the response time of the pressurised aerosol, the simple handling and the associated lower costs.
Positive effects on economic efficiency, environmental friendliness and occupational safety
However, the MQL can do much more and also has a very positive financial impact: All supply and disposal technology for the cooling lubricant is eliminated, tool life is optimised and the process duration is reduced by up to 30%. In addition, the KS no longer needs to be inspected and maintained and cleaning of the workpieces is reduced. And it also makes ecological sense: no environmentally harmful used emulsions are produced and accidents caused by leaking coolant are no longer possible. The MQL is also a big plus for occupational health and safety, as a dry machine environment increases work safety and illnesses caused by KS, e.g. respiratory illnesses, are also a thing of the past. So are there only advantages? Not at all, because the daily challenges are complex. The elimination of water ultimately means that the machining area is no longer cooled, the chips are no longer "washed away" by the KS, but remain stuck in the machine or on the workpiece or tool, and the supply of aerosol through the machine, chuck and tool is not easy either.
MMS as a future-proof technology from BILZ
So what needs to be done and what does this mean for a leading chuck manufacturer like BILZ? To put it simply: the adaptation of all components to MQL processing, by all parties involved:
-In terms of the machines, new technology is needed in the removal of chips and the supply of aerosol.
-The cutting parameters of the machining programmes must be configured in such a way that no overheating occurs.
-Modifications to the cooling channels of the tools may be necessary.
-The chuck itself must ensure that the aerosol is safely channelled through and the aerosol itself must be safely supplied by the MQL devices.
These are major and diverse requirements that BILZ faces every day in order to work on the optimum and, above all, future-proof solution for the customer. This makes it all the more important to think ahead with its unique technological modular system and to reach the necessary patent and licence agreements with all leading MMS system manufacturers at an early stage in order to be able to use the relevant systems. This applies in particular to the central MMS patent for the connection in the lining from HORKUS in Japan. BILZ has acquired the licence here in order to always offer our customers the most future-proof technology as a reliable partner.
Contacts
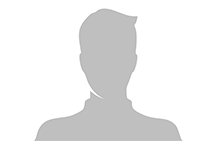