프로파일 가공 / 다각형 드릴링
폼보어 시스템 툴로 다각형 또는 자유형 모양 만들기
설명 / 특징
적응력과 독립성이 뛰어나며 설득력이 있습니다: Formbore 시스템 공구를 사용하면 처음으로 기존 머시닝 센터에서도 드릴링과 선삭만으로 내부 및 외부 윤곽뿐만 아니라 다양한 형상의 프로파일을 최대한의 정밀도로 다양하게 생산할 수 있습니다.
기계 스핀들과의 동기화를 계산하고 프로그래밍할 필요가 없습니다. 폼보어 시스템 툴은 다양한 프로파일 모양과 크기에 맞게 설계할 수 있습니다. 브로칭, 에로딩 또는 밀링과 같은 가공 공정을 변경할 수 있습니다.
폼보어 시스템 공구는 기존 방식에 비해 가공 시간을 크게 단축합니다. 또한 잔류 칩이 없는 블라인드 홀 드릴링 또는 절삭날 마모를 보정하여 영구적인 치수 정확도 등의 추가적인 장점도 제공합니다. 머시닝 센터 및 밀링 머신에서 사용할 경우, 토크 지지대와 모듈식 공구 홀더는 입증된 빌츠 탭핑 어태치먼트 유형 GNCK / GNCN과 동일합니다.
Formbore 시스템 공구의 설계 및 작동 방식
Formbore 시스템 공구는 기본적으로 드라이브와 드릴 헤드의 두 가지 구성 요소로 이루어져 있습니다. 회전 드라이브 샤프트는 하우징에 장착됩니다. 토크 지원 포지티브 제어는 드릴 헤드의 동작 순서를 정의합니다. 절삭 날의 편향은 순전히 롤링 요소에 의해 생성됩니다. 따라서 폼보어 시스템 공구는 마모가 거의 없고 유지보수가 필요 없습니다. 최대 900N/mm2 강도의 거의 모든 소재를 가공하는 데 적합합니다.
내부 가공의 경우, 플랫(SW) 폭보다 최대 직경이 0.5mm 작은 파일럿 홀이 먼저 생성됩니다. 그런 다음 실제 금형 구멍은 프로파일에 적합한 속도와 재료에 적합한 이송 속도로 한 번의 작업으로 드릴링됩니다.
Formbore 시스템 툴은 일상적인 작업에서 실용적인 다목적성, 유연성, 시간 및 비용 절감을 위한 시스템입니다. Formbore 시스템 툴의 장점을 직접 확인해보세요! 가공 요구 사항을 알려주시면 즉시 공구 추천을 받으실 수 있습니다.
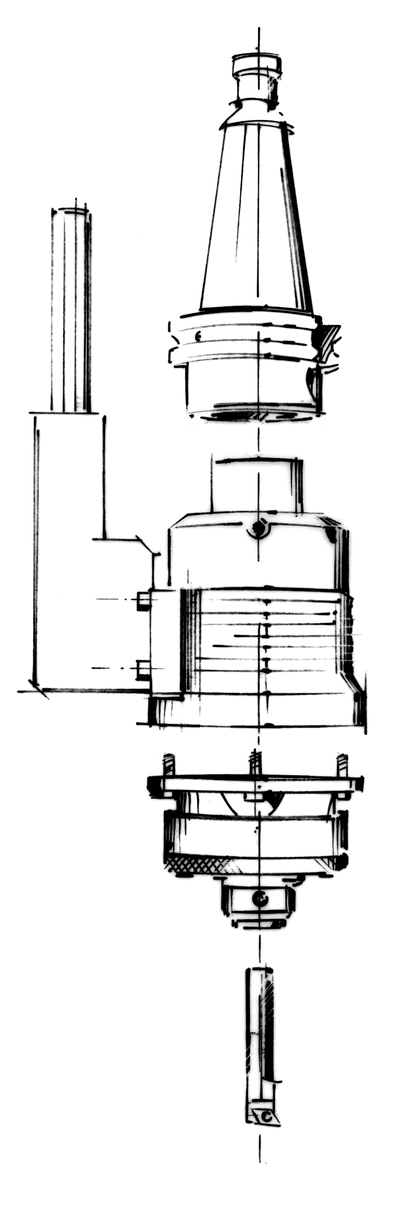
자주 묻는 질문 / FAQ
밀기에 비해 장점
- 측면은 항상 직선입니다(슬롯을 사용하면 각도가 매우 작아야 함).
- 높은 표면 품질
- 공차 품질 H11의 정확한 컨투어 형상
- 멀티 뱅 머신에서도 쉽게 사용 가능(공간 절약)
- 기계의 마모가 매우 낮음
- 블라인드 홀을 위한 깨끗한 보어 베이스
- 한 번의 클램핑 작업으로 공작물 생산 가능
폼보어 시스템 툴로 어떤 프로파일을 생산할 수 있습니까?
표준 형상은 다음과 같습니다.
- 정사각형
- Six-edge
준표준 금형은 다음과 같습니다.
- 실린더 표면
- 키 면
- 팔각형
- 다각형
특수 모양은 다음과 같습니다.
- 마름모
별(예: 십이각형)도 생성할 수 있습니다. 십각별은 2개의 육각형처럼 취급되므로 두 번의 절단이 필요합니다. 첫 번째 절단이 완료되면 공작물의 위치가 조정됩니다. 그런 다음 두 번째 절단에서 공작물이 완성됩니다.
폼보어 시스템 공구로 무엇을 어떻게 가공할 수 있나요?
형상과 재료에 따라 달성 가능한 정확도는 최대 0.03mm입니다.
공차, 플랫 너비(SW)를 통해 측정됩니다. 크라운은 약 0.02mm입니다.
모서리 반경은 다음과 같이 고려됩니다:
- 정사각형: 모서리 반경 SW의 10%
- 육각형: 모서리 반경 SW의 4%
더 작거나 더 큰 모서리 반경도 가능하며 이미 생산되고 있습니다. 절단 조건에 대한 개별적인 계산과 테스트가 필요합니다.
절삭 바디 또는 보링 강재의 절삭 형상을 변경해야 할 수도 있습니다. 이에 대한 분석 및 정보는 특정 요청 시 제공됩니다(고객 도면 필요).
사이즈 1 폼보어 시스템 공구의 경우 가공 깊이는 최대 35mm이고, 사이즈 2의 경우 가공 깊이는 최대 50mm입니다. 외부 가공의 경우 고객의 요구 사항을 확인해야 합니다.
금형의 위치를 결정할 수 있습니다. 예를 들어 육각형이 팁에 있는지 또는 표면에 있는지 여부를 결정할 수 있습니다. 선반에서 이 위치를 결정하는 가장 쉬운 방법은 스핀들의 방향을 지정하는 것입니다. 또한 하우징의 드라이브 헤드를 움직여 공구를 제어된 방식으로 쉽게 재배치할 수 있습니다.
달성된 치수는 수정할 수 있습니다. 폼보어 시스템 금형에는 +/- 0.2mm의 조정이 가능한 스케일링된 편심 부시가 있습니다. 대형 금형의 경우 보링 바의 특수 조정 나사를 사용하여 조정할 수 있습니다.
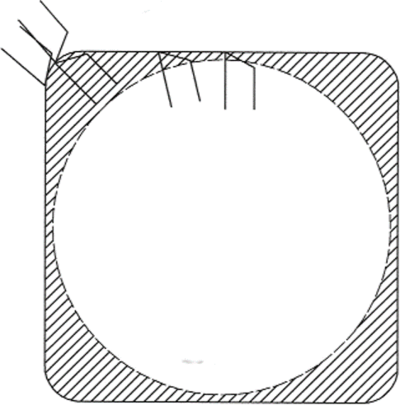
폼보어 시스템 툴로 마무리하기 전에 어떻게 사전 가공을 수행해야 하나요?
닫힌 프로파일이 필요한 경우 내부 프로파일의 경우 공칭 치수보다 0.5mm 낮게 가공하는 것이 좋습니다.
내부 프로파일의 경우 공칭 치수보다 낮게 가공하는 것이 좋습니다.
외부 가공의 경우, 원시 치수는 가장 큰 완성 치수보다 0.5mm 위에 있어야 합니다.
커브 블록과 보링 바는 몇 개가 필요합니까?
폼보어 시스템 공구는 캠 블록에 의해 편향되는 기계적으로 제어되는 공구로 알려져 있습니다.
원칙적으로 각 프로파일과 프로파일의 크기마다 별도의 캠 블록이 필요합니다.
또한 다른 보링 스틸 또는 전복 스틸을 사용해야 합니다.
그러나 정사각형과 육각형 및 기타 형상 모두에 동일한 폼보어 스틸을 사용할 수 있습니다.
사용자가 직접 캠 블록을 교체할 수 있나요?
예. 배송 시 커브 변경에 대한 사용 설명서를 함께 제공합니다.
커브 변경에는 약 5분 정도 소요됩니다.
사용자는 어떤 캠이 설치되어 있는지 어떻게 알 수 있나요?
폼보어 시스템 금형의 드라이브 헤드에 디스플레이 창이 있습니다. 캠 블록의 지정이 여기에 표시됩니다. 캠 블록을 위한 코딩 시스템이 개발되었으며, 이는 별도의 워크시트에 자세히 설명되어 있습니다.
사용 중 준수해야 할 사항은 무엇인가요?
폼보어 시스템 공구에는 속도 제한이 적용됩니다.
- 사이즈 1: 최대 1000분-1
- 사이즈 2: 최대 500분-1
참고:
속도 제한은 작동 및 공회전 모두에 적용됩니다!
후자의 제한은 중앙 드라이브가 있는 터렛이 있는 선반에서 폼보어 시스템 공구를 사용할 계획인 경우 특히 중요합니다.
내부 및 외부 윤곽을 동일한 방식으로 처리해야 합니까?
우선, 하나의 동일한 폼보어 보링 헤드와 폼보어 캠 블록을 정의된 프로파일의 내부 및 외부 가공에 모두 사용할 수 있습니다.
사용할 수 있습니다.
차이점은 폼보어 보링 공구 또는 폼보어 선삭 공구의 선택에 있습니다.
외부 가공에는 감소된 값을 사용해야 합니다. 가공 공정에 따라 공구의 비틀림을 방지하기 위해 전복 길이를 부분적으로 줄여 공구를 안정적으로 유지해야 합니다.
폼보어 시스템 공구와 함께 절삭유를 사용할 수 있나요?
예. 모든 폼보어 시스템 공구에는 외부에서 공급되는 절삭유가 폼보어 헤드에
폼보어 헤드에 들어가는 것을 방지하는 씰이 있습니다. 이 씰은 칩의 유입도 방지합니다.
내부 절삭유 피드스루를 위한 변형은 계획되어 있지 않으며 의미가 없습니다.
처리 예제
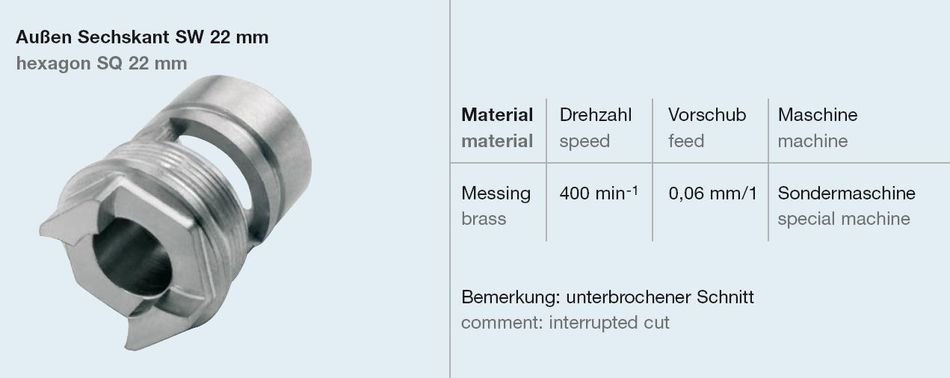
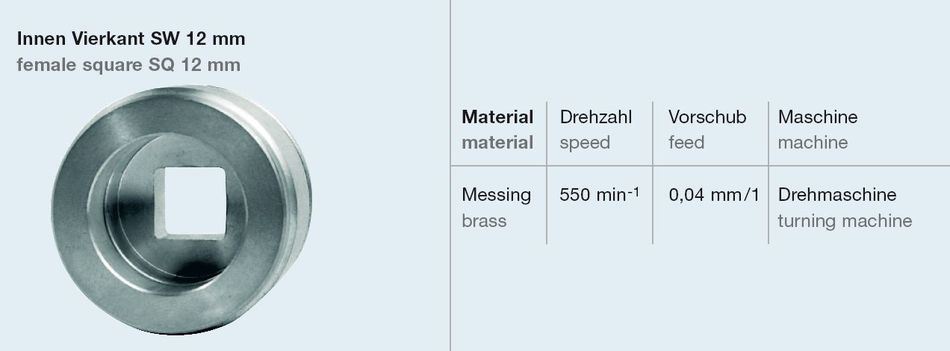
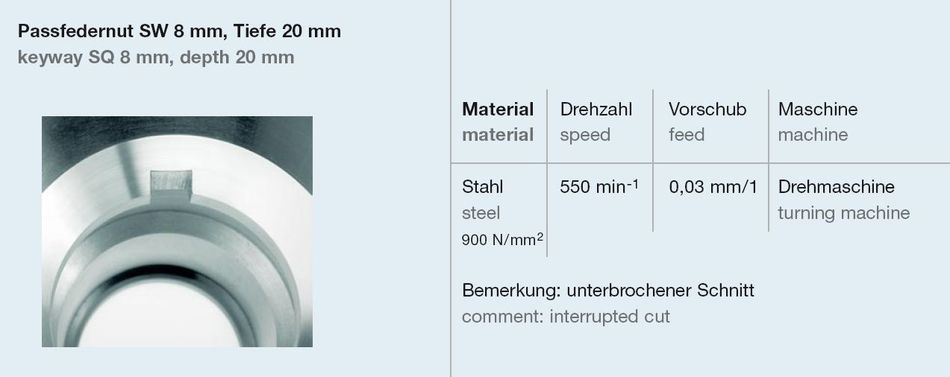
담당자
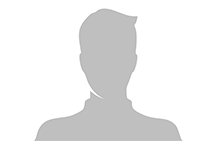
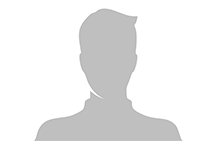